Sustainability policy
Challenges for the future
In accordance with the Group Management Philosophy,
we aim to be an essential company that contributes
to social progress and harmony with the global
environment, while continuing to move forward
through resource circulation business to contribute to
realizing a sustainable society.
Given that our aim is to become an Essential Company that contributes to both social progress and harmony with the global environment, having sustainable management is absolutely essential. So that we can put our Sustainability Policy into practice, under the supervision of the Board of Directors we need to identify management issues, risks, and opportunities in light of both the Group’s business situation and the external business environment, and formulate responses to these. Issues identified as of particular importance are incorporated into our medium-term business plan, as materialities, and we have established specific initiatives and KPIs.
In order to achieve these KPIs, the Company established a company-wide management structure, each business operations division handled their issues through discussions in each committee and subcommittee, and we accelerated initiatives.
Materialities are reviewed when necessary, with business risks and opportunities impacting the Group discussed and reviewed annually by the Corporate Risk Management Committee.
- 拡大
- Positioning of the Sustainability Policy
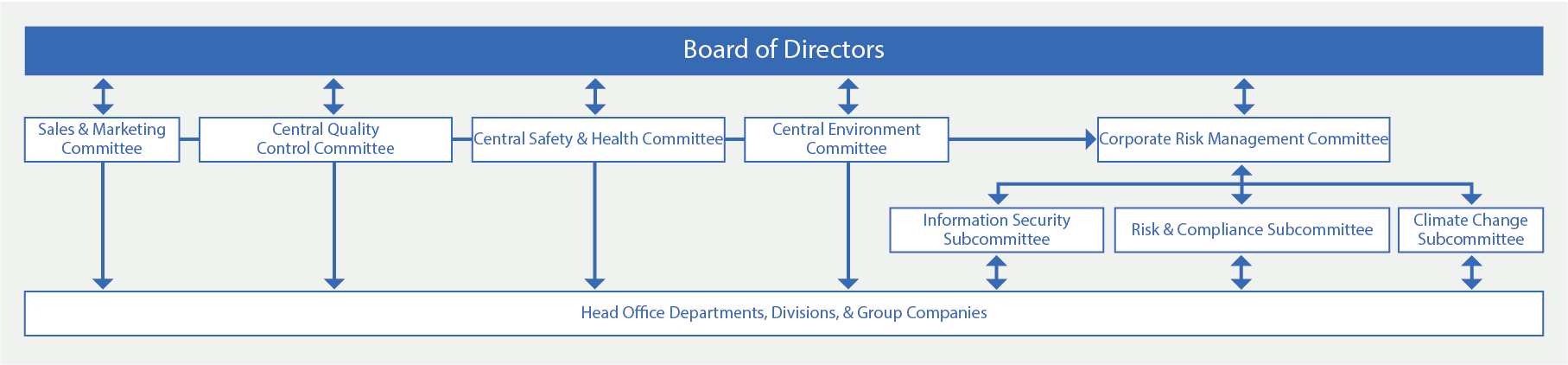
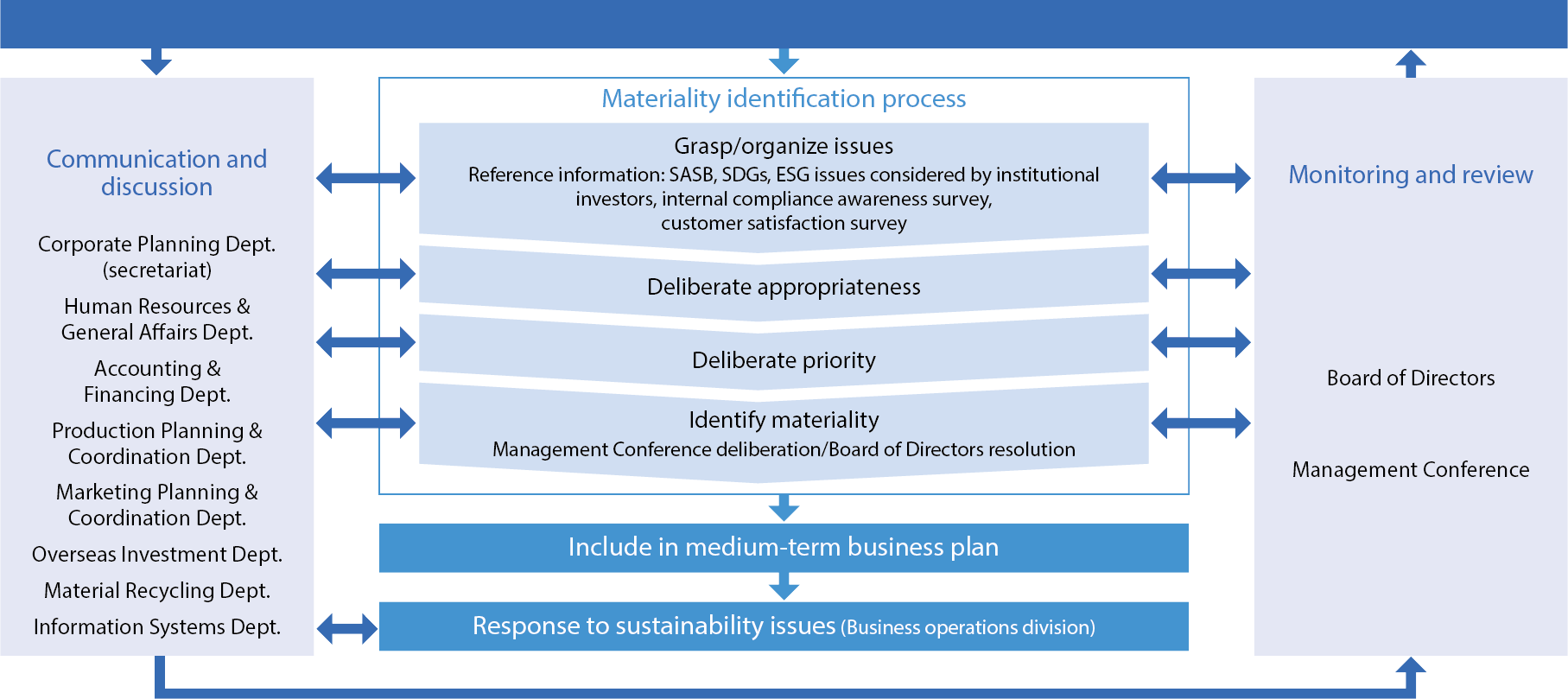
Sustainability issues |
▼ Risks ▲ Opportunities |
---|
Climate |
▼ Increased capital investment to comply with stricter greenhouse gas emission regulations. ▼ Increased costs due to the introduction of carbon pricing. ▼ Suspension of operations due to abnormal weather conditions caused by climate change etc. ▼ Suspension of operations due to natural disasters. ▲ Formation of new product markets through reputation gained by further contribution to resource circulation business. ▲ Increased demand and sales opportunities for products with low CO2 emissions (steel production using EAFs, green steel, and carbon footprint-labeled products). ▲ Increased demand and sales opportunities as a national resilience product against natural disasters. ▲ Increased demand for discrete products such as threaded rebars and assembled products for precast concrete, because labor savings on construction sites are required due to rising average temperatures. |
---|
Steepening |
▼ Workforce population decline resulting in an increasingly serious shortage of personnel. |
---|
Constraints on |
▼ Increased costs due to advancing greenflation. |
---|
Energy |
▼ Increased difficulty in obtaining energy resources (LNG and other low CO2 emission fuels) are becoming more difficult to obtain, with higher prices. |
---|
Changes in |
▼ Decreases in sale prices and shipment volumes due to excess domestic supply capacity. |
---|
Acceleration of a |
▼ Information leaks and system failures due to cyber-attacks and system abuse. |
---|
We have identified materialities that our Group should address using repeated evaluation and analysis of issues identified on the basis of the level of importance from stakeholders’ perspectives. The six materialities are incorporated into our medium-term business plan, and we are working to achieve the ideal state of our Group through our business activities.
- 拡大
- Our approach to materialities
Materialities |
KPI in NeXuS II 2026 |
Concrete measures |
|
For a comfortable and safe society |
We will contribute to global environmental conservation and support the global infrastructure by recycling resources after they have finished their roles in people’s lives. |
● Net sales: ¥380 billion ● Operating income: ¥25 billion ● Shipment volume: 4.0 million tonnes (domestic: 1.6 million tonnes; overseas: 2.4 million tonnes) |
[Domestic steel] ● Increase presence in the Kanto region ● Strengthening of processed product business (downstream strategy) ● Stable procurement of scrap (upstream strategy) ● Continuation of initiatives to increase added value [Overseas steel] ● Strengthening profitability by shifting the weight of our tripolar structure: Emphasis on North America, reinforcement of northern Vietnam [Material recycling] ● Branding of the uniqueness of the business ● Reinforcement of industrial waste treatment network |
Toward a beautiful global environment |
We will not only reduce greenhouse gases and byproducts produced by the Group, but we will contribute to realizing a society that has less impact on the environment by recycling various kinds of waste generated by society. |
● Reduction of CO2 emissions by 50% from FY2014 by FY2031 ● Improvement of energy intensity by 1.0% per year |
● Initiatives to reduce CO2 emissions at overseas related companies ● Conversion to fuels with low CO2 emission factors • Promotion of energy saving at each site • Fuel conversion • Photovoltaic power generation • Initiatives to reduce CO2 emissions at overseas sites ● Making effective use of slag and dust |
To meet the expectations of everyone who creates value along with us |
We intend to contribute to society through our value chain by providing products and services that meet the varied expectations and requests of our customers and business partners, as well as by procuring raw materials and processed materials that have a low impact on the environment. |
● Promoting support for processing departments and processors ● Expanding treatment of industrial waste, which is expected to increase in the future ● Reduction of waiting times for product loading |
|
Toward safer and more comfortable workplaces |
We will create safer, more comfortable, and more appealing workplaces by eliminating occupational injuries, improving working environments, hiring diverse human resources, and adopting flexible working styles. |
● No occupational injury ● At least 15% female career-track employees (non-consolidated) ● At least 3.0% females in managerial positions (non-consolidated) ● Education and training costs: 150,000 yen/person (non-consolidated) |
● Improving the level of safety and stable operation of each plant by strengthening engineering departments ● Introducing AI into raw material inspection and production processes ● Promoting automation in production processes ● Implementing concrete measures based on the human capital strategy |
To contribute as a member of the community |
We aim to make the Group indispensable to the community by contributing through various activities, including disaster prevention. |
● Social contribution activity expenditures: Approx. 0.5% of consolidated net income |
● Contributing to local communities through olive grove planting ● Continuation of donations through regional social foundations, MESSCUD Medical Safety Fund and other organizations |
Toward fairer and more sincere corporate activities |
We aim to earn the trust of society by building an organizational structure and a highly transparent management system that quickly respond to changes in the business environment, as well as by practicing fair and sincere corporate activities. |
● To be continuously listed in the new market segment (Prime Market) of the Tokyo Stock Exchange |
● Functional enhancement of the board of directors (enhancement of the skills matrix) ● Reinforcement of risk management system ● Review of the structure of each committee |